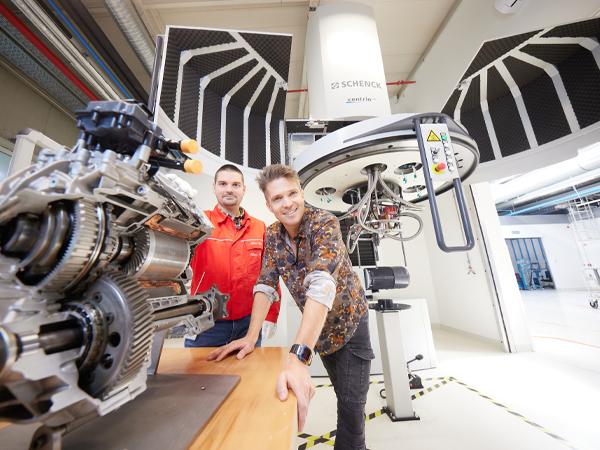
Aaaaaand action!
Behind the scenes at Technical Development
Over the course of two days at Technical Development, we will see extreme temperature conditions, climactic vehicle test benches, soundproofed units and rotors spun to breaking point. The popular Hungarian vlogger Csaba Gyetván and his crew are collecting trade secrets and behind-the-scenes material for the Discovery Channel. Let the factory tour begin!
For most of us, our everyday lives would be unimaginable without a reliable car. But how much expertise does it take – and how many hundreds of thousands of test cycles – to ensure all those millions of starts and stops and all that accelerating and braking proceeds as smoothly as we have come to expect? We don’t even think about it, of course – we don’t usually see acoustic engineers utilising cutting-edge technology to measure the noise levels of the bodywork in examination cabins, and most of us have no idea that having a perfectly running car is the fruit of the thousands of hours spent by simulation engineers in front of a monitor. Now, however, we can enjoy a glimpse backstage. As we enjoy our morning coffee at Technical Development – the third largest development centre at AUDI AG – a lively discussion is underway. Photographers and cameramen are fine-tuning the shooting locations with the TV presenter Csaba Gyetván, host of the ‘Hogyan készül?’ (‘How Is It Made?’) videos. The vlogger presenter and his crew are shooting upcoming episodes for the ‘Made In, with Csaba Gyetván’ Discovery Channel series, and the subject is the technical development taking place at the Audi factory. Monday morning, 9 am and everyone and everything is ready to go. Let the cameras roll!
Quiet on the set please!
We begin in Vehicle Development, passing endurance testers and roller test benches as we approach our first stop, the acoustic hall. From the outside, it looks like an enormous vault: the space is closed off by a half-metre-thick door, whose soundproofing material prevents soundwaves from reverberating off the walls. The ventilation system also has noise-insulation, while the hall is fitted with an exhaust fume extraction system for when engine tests are being carried out. The goal they are working towards is to reduce the level of noise of the cars when driving, and also to eliminate these noises from the cabin space. “If we don’t get it right, the bodywork will sound something like a loudspeaker,” explains acoustic development engineer Dr. István Antal Horváth. He is standing next to the body of a car as he examines data sent by a laser scanner, which is directed at the bodywork and provides an image of the soundwaves. At times, sounds ring out in the hall that remind us of the classic Andrei Tarkovsky film Solaris, while at other times it feels more like listening to a lullaby. István records every piece of data.
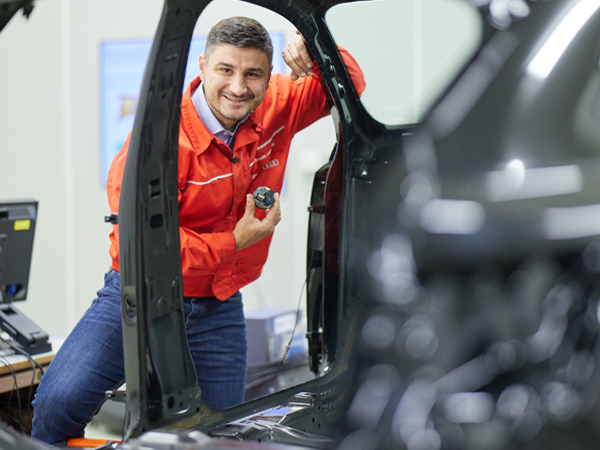
If we don’t get it right, the bodywork will sound something like a loudspeaker.
Watch out, centrifuge up and running!
We return from the overwhelming silence to the world of sounds and the spinning parts testing centrifuges (SPSs), a short walk from the acoustic hall. The machines, all 4-5 metres tall, are used for rotor spin tests, cycle tests and durability tests. In the centrifuges, the engineers simulate the response not only to different real-life situations, but also the load expected across the entire product life, while they also assess the endurance of the rotor – which is the heart of the motor in electric cars. Development engineer Mátyás Dobos explains the testing methods. “During the spin test, we measure how the rotor changes shape. In the centrifuge, we reproduce operational conditions, then use sensors to record data every second across 180,000 points of measurement. The cycle test is different: in this phase, we spin the rotor 24 hours a day for two weeks: we want to subject it to far more rotations than when it is used by customers. We want to know how the rotor will react to extreme strain. Finally, the durability test puts the rotor under strain until it breaks.” Try to imagine the extreme conditions needed to break a steel part weighing several kilos! After they fix the rotor in place, the centrifuge is closed. As the number of rotations per minute increases, the ceramic sheets placed around the fixed unit heat up to 130-180 degrees. By the end, the rotor is spinning at an extremely high speed, and in the vacuum it finally gives up the fight. The system immediately shoots nitrogen into the centrifuge in order to prevent any sparks. The inner layers of the centrifuge, which are a few centimetres apart, are protected by three half-tonne steel rings, and when it breaks, the fragments of the rotor become embedded in the innermost section. “The impact is so powerful that it is capable of shifting the first steel ring from its position. Our measurements indicate that some rotor fragments hit the ring at Mach 1 – the speed of sound,” Mátyás tells us to convey the scale of the forces at work. The two centrifuges are a significant advancement. Whereas the Volkswagen Group had previously only been able to carry out these kinds of tests with external companies, now the technology is available in house. We should point out, however, that this process would never occur under normal conditions: in the hands of our customers, the car engines will be subjected to a significantly lower rate of rotation.
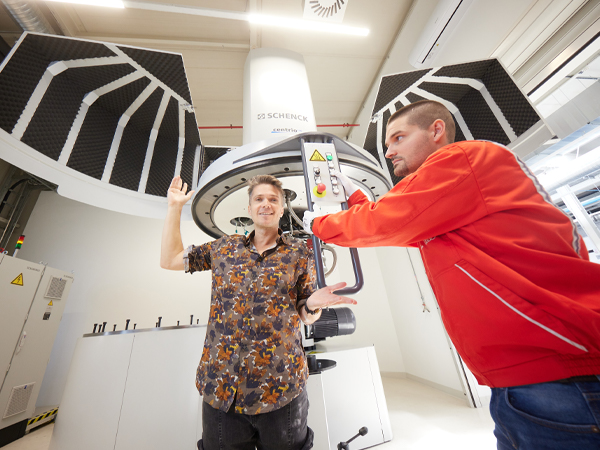
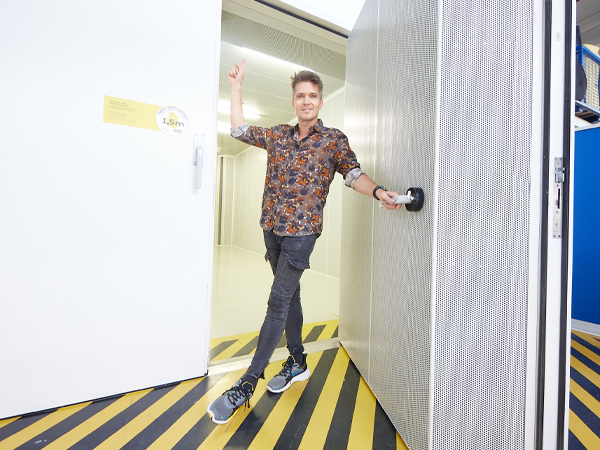
Can the system take it?
Our next location is the roller brake test bench. We step into the room to see three experts observing a shapely Porsche on a monitor screen. The test subject is resting on the roller brake test bench for vehicle testing, as two enormous fans create an artificial wind around it. It’s as though the car were driving through mountains and valleys, while the gear changes recreate the stop-start pace of urban traffic jams. The 160-tonne brake test bench lies on steel spirals fitted under the floor, where you will also find the electric motors that power the fans, which are capable of generating winds of up to 130 km/h. The test objective: to check how the exhaust system and new parts operate under extreme strain, as well as at maximum speed (280 km/h), with specific pieces fitted with strain gauges and accelerometers. The engineers also look for sounds and vibrations produced when the car is running. The wall is soundproofed here, too, as the roller brake bench is also used for acoustic measurements, where the rolling sounds of the vehicle are measured for hours or sometimes even weeks at a time.
The engineers also look for sounds and vibrations produced when the car is running.
Engine control? All good!
At the HiL (Hardware in the Loop) lab, Gábor Ferenc Takács and László Kajcsos welcome us to a place that closely resembles a server room. Gábor and László are responsible for testing – with mechanical assistance – the complete engine control network in the early stages of development. Their work enables us to collect information that can be used in further development prior to the official vehicle tests. “Because it wouldn’t be economical to do production tests on all the different kinds of vehicles made by Audi, experts have developed equipment that enables us to test the electronics for each individual internal combustion engine and electric motor. The machines also carry out sensor and strain-based simulations, and test connectivity to the control unit,” explains the simulation engineer. Interestingly, the same technique is also used in the airline industry and in space research. By the end of the day, our heads are buzzing with all the information received and things we have seen, but we can hardly wait for the following day. The Technical Development Powertrain Development team have promised even more action-packed activities and similarly fascinating sights!
How powertrains are born
We begin our second day in the Powertrain Development office building in the company of András Doór, technical coordinator for the acoustic team. He quickly gets to the point: “AUDI AG creates the concept, then here in Győr we develop it until it is ready, make the powertrains and then the process ends with the final product itself.” As we speak, we stroll across the hall past a 3.0-litre Audi S5 TFSI engine. It’s hard not to linger; we would gladly gaze at it for hours, but we have to press on – the schedule is tight.
We quickly make our way to the design engineering department, where parts are being designed in a 3D environment. Our colleagues working here, however, not only design the part in question, they also follow it for the entirety of its lifecycle, which requires keeping in touch with test engineers, production design, procurement, control, quality assurance, logistics and the relevant areas of production. Dániel Michl is waiting for the crew – as a constructor, he is responsible for designing electric drives. When we arrive, he is in the middle of examining the drive for an e-tron SUV on the monitor. In response to questions from Csaba, our reporter, Dániel begins to explain the most typical processes in his work. “Though we are mainly focused on design, what we do from day to day depends on the task at hand… A project might begin with the further development of an existing internal combustion engine or an electric powertrain, or it might start from zero. In the latter case, we are not developing the models of the previous generation, but an entirely new concept. Naturally, we can still apply our previous knowledge and experience. For buyers, the car’s performance and (cost) efficiency are still the most important factors – as well as range, in the case of electric cars, of course” he explains. The team designs everything with these criteria in mind.
Just like in the movies
In a slight diversion from our visit to Technical Development, Dániel also accompanies us to the electric powertrain assembly area, undoubtedly one of the most spectacular sights in the factory. As we enter, we are captivated by the sight of driverless electric transport vehicles (FTF – Fahrerloses Transportfahrzeug), which look like something out of Star Wars. There are 36 of them in total, all moving completely independently about the plant, with no human supervision. We will soon be ‘introduced’. After welcoming the team, project manager, Attila Józsa informs us that, in addition to the FTFs, there are also 330-340 staff working in the assembly area across three shifts. Made here every day are no fewer than 530 stators, which are later fitted to the electric drive of the e-tron SUV. In the next stage, the rotor, bearings, seals, gearbox and other essential parts are connected to the stator, before the finished power unit goes to the test bench and finally to Brussels, where it is fitted into the car. But let’s return to the transport vehicles – known as ‘dogs’ – which help the entire production process run smoothly. They transport the parts and sections of the motor between the different production islands, and curtly let us know if we get in their way. With a single charge, they are able to travel along designated lanes for three to four hours, before plugging themselves back into the charging point. Information from all the machines in the assembly hall is fed into a central programme, which, based on the inputs received, instructs the transport vehicles which production island to go to next. It’s a real treat to meet them – you definitely don’t find this kind of technology in most car factories!
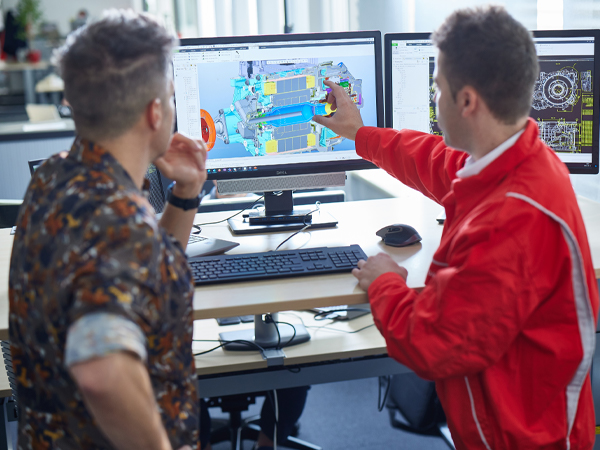
We make our way to the design engineering department, where parts are being designed in a 3D environment.
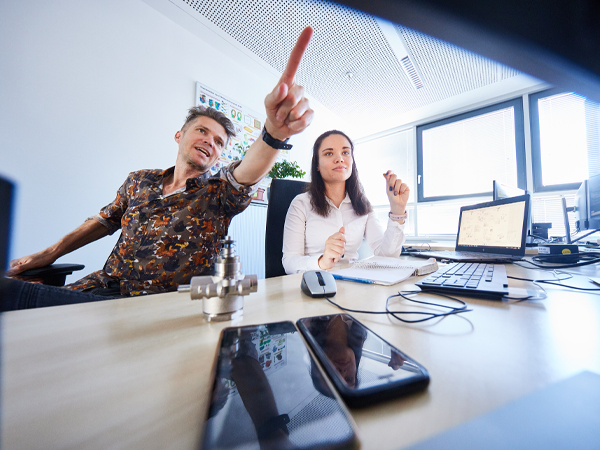
Simulations instead of tests
We have no time to rest, however – a few minutes later we are standing in front of a monitor that belongs to one of the simulation engineers: Beatrix Sipos is carrying out numerical simulations based on the loads expected during real-life use. Together with her team, she is looking to find out whether a part will break under a certain amount of strain, for example. “This work can save us a lot of resources, time and money,” she explains, and this is no exaggeration. The numerical simulation is a substitute for some of the brake test bench and vehicle tests, as it can tell us the expected product life duration of individual parts in advance.
Another noise test
If there is one place where you can’t skimp on the testing, it’s definitely the acoustic brake test bench. Next to a Lamborghini engine in a soundproof room, experimental engineer Viktor Rőfös-Horváth and our earlier acquaintance András Doór explain how the next test works. With the help of accelerator sensors and microphones, they test the noise level and vibrations of the running engine for hours. Then, based on the results obtained under various real-life conditions, the team decides if the engine – taken either from the production line or an operating car – is okay, and, if not, what part is causing the problem.
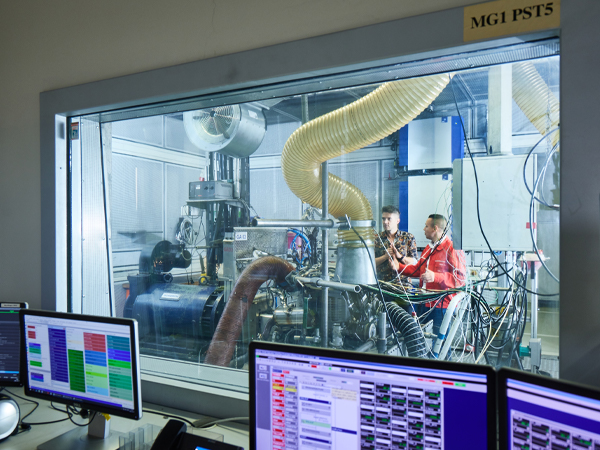
Extreme conditions
The last stop and filming location on our factory visit is also situated in the test centre. It is the site for long-term tests, where heat alternates with freezing cold in a row of cabins: climatic tests are carried out on the power sources used in the hybrid powertrain across 14 climate cabins, with temperatures ranging from +40 to -40 degrees Celsius. We enter a cabin set to -28 degrees, accompaniedby development engineer Ákos Balics, who informs us that the demand for hybrid power sources is much higher in northern countries, which is one of the reasons they test them at these temperatures. Because theengine stops and starts regularly with hybrid vehicles, extreme tests are required, encompassing frequent changes to the temperature and other parameters. In the cabin, the engine of the drive is restarted every few seconds, 24 hours a day. Some engines run for 100,000 kilometres over 12 weeks. “This is one of the most comprehensive start-stop tests. The system carries out 3,000 start-stop cycles a day, and the test consists of 250,000 cycles in total. In the meantime, of course, we change the oil filter,air filters and the spark plugs, and also monitor the engine characteristics, frequencies, engine control and parts. We have to react immediately to any problems that arise when the engine is running. No two working days are the same, which is what makes our work so magical,” the expert informs us from in front of the test bench monitor as we listen in fascination.
Based on all that we have seen and heard by the end of our two-day tour of discovery, we can safely say that Audi Hungaria is showing no signs of slowing down – quite the opposite! In the next few years, the company will invest tens of millions of euros into Technical Development. The investment will see a new brake test bench fitted for the development of electric axle drives and their transmissions, while the existing brake test bench infrastructure will also be upgraded to ensure it can make an even bigger contribution to the future of mobility – from Győr to the world.