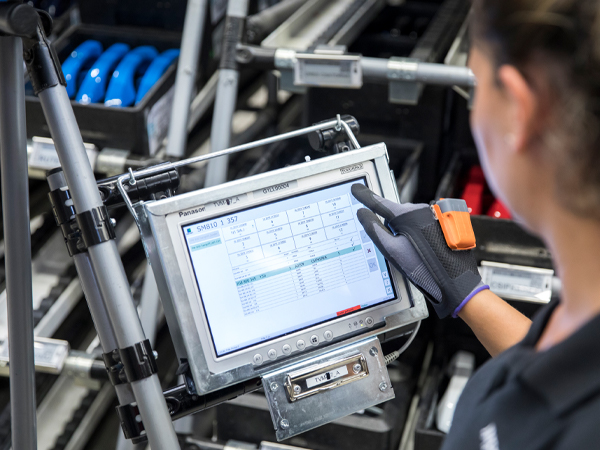
Entwicklungen bringen uns weiter
Innovationen, auf die wir stolz sind
Digitalisierung, Automatisierung und Nachhaltigkeit spielen im Alltag von Audi Hungaria eine große Rolle. Sie haben das Ziel, unsere vielfältigen Tätigkeiten schneller, sicherer und präziser zu machen. Oft ermöglichen dies eigene Ideen und Entwicklungen – von cleveren Robotern bis hin zu smarten Tools und passender Software. Das sind drei herausragende Beispiele:
Mensch-Roboter-Kooperation im WerkzeugbauIn unserem Werkzeugbau entstehen hoch präzise Karosserieteile für Exklusivmodelle des Volkswagen Konzerns – und auch viele neue Ideen zu ihrer Produktion: Türen, Kotflügel, Motorhauben, Kofferraumdeckel und Seitenwände werden inzwischen in flexiblen Roboterzellen gefertigt. Denn bei so vielen Konfigurationsmöglichkeiten, wie sie die anspruchsvollen Premiumkunden haben, steigt im Effekt auch die Nachfrage nach digitalen Lösungen und zukunftsweisender Automatisierungstechnik. Dazu haben unsere Mitarbeitenden im Bereich Anlagen- und Vorrichtungsbau im Sommer 2022 eine innovative Technologie in Betrieb genommen: eine kollaborative Roboter-Klebestation, die von unseren Anlageningenieur_innen in Zusammenarbeit mit den Spezialist_innen für kollaborative Roboter der AUDI AG entwickelt wurde.
Dabei kommt das Beste aus zwei Welten zusammen – der menschlichen und der technischen: Das Besondere an der neuen Technologie ist nämlich, dass die Zusammenarbeit zwischen Mensch und Roboter nicht mehr räumlich voneinander getrennt ist. Anders als bei herkömmlichen Industrierobotern, ist hier kein Schutzzaun erforderlich; die Kolleg_innen arbeiten sicher und direkt neben dem Roboter, sozusagen Hand in Hand. Während des Arbeitsprozesses bereiten Mitarbeitende dazu die Teile vor. Dann drücken sie den Startknopf, um den Klebevorgang zu starten. Kollege Roboter führt diesen Arbeitsschritt dann aus. Vom Einsatz der neuen Arbeitskraft profitieren alle in der Schicht. Denn die Prozesse werden dadurch stabiler, die Qualität des Klebebildes wird erhöht, und die Mitarbeitenden sparen durch die Optimierung der Teilevorbereitung etwa vier Kilometer Wegstrecke pro Schicht.
Es ist übrigens nicht das erste Mal, dass die Expert_innen auf diesem Gebiet ihre jahrzehntelange Erfahrung im automatisierten Roboterzellenbau nutzen. Bereits im Dezember 2020 wurde ein für das Antriebsfertigung konzipierte Roboterzelle in Betrieb genommen, der Aufgaben bei der Produktion von Vierzylinder-Ottantrieben übernimmt: Der starke Unterstützter hebt ganze Motorblöcke mit einem Gewicht von fast 30 Kilogramm von einer mehrstöckigen Rohmaterialpalette auf die Produktionslinie, wobei er die Trennelemente auch einzeln sortiert. Damit reduziert der Roboter die Risiken für die Arbeitssicherheit und verbessert die Ergonomie der Arbeitsplätze seiner menschlichen Mitarbeitenden.

Genau hingeschaut und vorgewarnt – das macht Produkte noch besser: Ein Team von drei Ingenieuren aus unserem Motorenanlaufzentrum hat dazu in Zusammenarbeit mit der Lackiererei eine Kamerastation entwickelt, die die Arbeit des Bereichs wesentlich erleichtert. Sieben hochauflösende, mit einem Mikrocomputer ausgestattete Kameras sind in 3-D-gedruckten Gehäusen untergebracht. Die Hightech-Augen werden in der PVC-Produktionslinie der Lackiererei eingesetzt und kontrollieren dort mehr als 150 Eingriffspunkte an der Unterseite der Karosserie. Dort werden entsprechend der schier unendlichen Zahl individueller Kundenkonfigurationen Stecker und Dichtungen eingesetzt oder müssen umgekehrt im Zuge der Fertigung entfernt werden. Die Kameras suchen ganz exakt nach Abweichungen, die zu Installationsschwierigkeiten oder Leckagen führen könnten. Schon in der Zelle vor dem Prüfpunkt werden dazu Fotos des eingehenden Teils gemacht; diese Bilder prüft das Programm in Echtzeit, wertet sie aus und sendet die Ergebnisse an die Steuereinheit. Jeder Fehler wird sofort den Kolleg_innen an der nächsten Station gemeldet. Nach einer intensiven Testphase ist das System hoch erfolgreich:Reklamationen in diesem Bereich gehören bereits jetzt der Vergangenheit an.
Zu den smarten Lösungen zählen zudem auch smarte Handschuhe. Sie werden in der Kommissionierung an der Montagelinie im Fahrzeugwerk verwendet. Diese Entwicklung stellt sicher, dass Teile auch bei einem geringeren Lagerbestand schnell und just in time an ihren Einbauort geliefert werden. Das funktioniert so: Für die Sortierung und Vorbereitung der Teile steht eine produktionsnahe Logistikplattform zur Verfügung – in diesem sogenannten Supermarkt arbeiten die Mitarbeitenden mit einer Sammelliste, die mehr als 150 Teilegruppen umfasst und auf einem Tablet eingesehen werden kann. Nachdem sie das erforderliche Teil ausgewählt haben, erfassen sie den QR- oder Barcode mit dem Scanner auf der Rückseite des smarten Handschuhs. Das System gibt blitzschnell Rückmeldung und die Bestätigung, dass das richtige Teil verschickt wurde. Diese Anwendung hat viele Vorteile: Sie ist schnell, kostengünstig, reduziert den Papierverbrauch und erleichtert die Arbeit.
Die smarte Handschuhe haben viele Vorteile: Sie sind schnell, kostengünstig, reduzieren den Papierverbrauch und erleichtern die Arbeit.
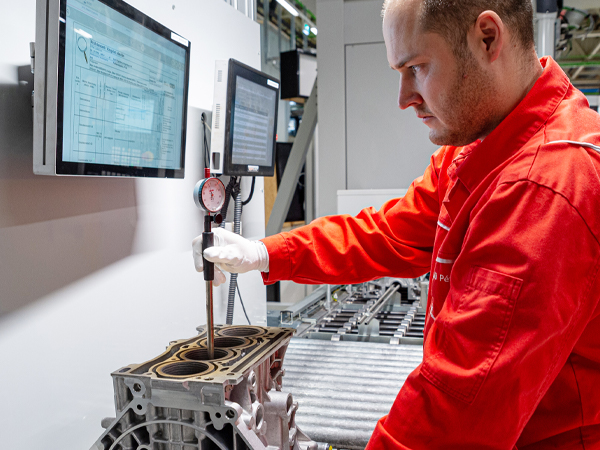
Elektroantriebe sind bereits eine starke Gegenwart und unsere Zukunft. Aber wir lassen auch nicht nach bei der Entwicklung und Nachhaltigkeit von Verbrennungsantrieben, die unsere Kunden noch viele Jahre nachfragen werden. Ein Beispiel dafür ist das proaktive Handeln im Rahmen zukünftiger Umweltvorschriften. Dazu haben wir die APS-Beschichtung (Atmospheric Plasma Spraying) entwickelt, um in den Zylinderbohrungen des Motorblocks eine mikroporöse, zehntelmillimeterdicke Stahlschicht zu bilden. Das sorgt für eine besonders gute Schmierung im Motor. Der Erfolg: Die innere Reibung wird weiter verringert, und letztlich werden CO2-Emissionen reduziert. Diese Innovation für eine grüne Zukunft wird im Volkswagen Konzern auch in Salzgitter eingesetzt. Audi Hungaria hat sie bei der Produktion von Motorblöcken für Fünf- und Achtzylindermotoren eingeführt.
Neben der konsequenten Weiterentwicklung der Verbrennungsantrieben arbeitet unser Antriebsfertigung mit großem Einsatz an der elektrischen Transformation und dem Ausbau der E-Kompetenzen. Schon am 24. Juli 2018 hat dies zum offiziellen Serienstart der Elektroantrieben für das erste reine Elektromodell von Audi, den Audi e-tron, geführt. Seit diesem Start ist das Werk in Győr inzwischen zum zentralen Produktionsstandort des Konzerns für elektrische Antriebe geworden – und hat eine Reihe von Meilensteinen auf dem Weg in eine grüne Zukunft gesetzt. 2020 startete die Serienproduktion der neuen Generation von Elektroantrieben, der Performance-Antriebsserie für die Audi e-tron S-Modelle, die von drei elektrischen Aggregaten aus Győr angetrieben werden.
Der Blick der Ingenieur_innen richtet sich aber bereits auf die nächste Zukunft. Denn das Unternehmen bereitet die Produktion einer neuen Generation von Antrieben auf der Premium Platform Electric (PPE) vor. Sie wird das derzeitige Portfolio von Hunderttausenden jährlich produzierter E-Antrieben signifikant bereichern. Der künftige Produktionsprozess besteht aus der Fertigung von Stator- und Getriebekomponenten und der Montage des Antriebsstrangs. Gerade die Fertigung der Getriebekomponenten stellt dabei eine weitere Innovation und Kompetenzerweiterung gegenüber der bisherigen E-Antriebs-Produktion dar.
Ein weiteres Novum ist, dass zur Planung der PPE-Produktionslinien erstmals in der Geschichte des Unternehmens VR-Brillen und die damit verbundene neue 3-D-Bildverarbeitungstechnologie zum Einsatz kamen.
Und die nächste Kompetenz- und Produkterweiterung ist bereits in Sicht: Ab 2025 werden in einem neuen Produktionsbereich MEBeco-Antriebe (Modularer E-Antriebs-Baukasten) für die kleinen Elektroautos des Volkswagen Konzerns produziert. Dadurch erhöht sich die Fertigungstiefe, da wir auch das Blechpaket, den Rotor und später sogar die Leistungselektronik herstellen werden.
Unsere Antriebsfertigung arbeitet mit großem Einsatz an der elektrischen Transformation und dem Ausbau der E-Kompetenzen.
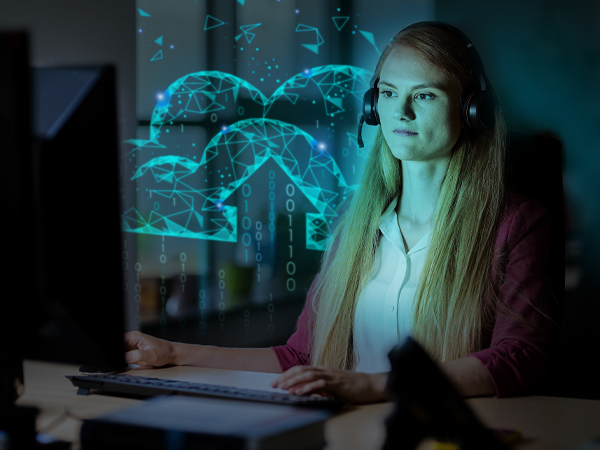
Die digitale Transformation zu unterstützen – das ist das Hauptziel der Plattform „Kubika“: Das ist eine von der AUDI AG entwickelte containerisierte Umgebung für sogenannte Multi-Tenant Public Cloud Services auf Basis des Open-Source-System Kubernetes. Was die Funktionalität betrifft, so können alle Nutzer_innen, die diese Plattform verwenden, ihre Anwendungen in der Cloud in verschiedenen Containern ausführen. Dafür bietet die Kubika- Infrastruktur eine zuverlässige, flexible und sichere Umgebung in öffentlichen Cloud-Diensten wie zum Beispiel Amazon Web Services (AWS), Microsoft Azure oder Google Cloud Platform und ermöglicht Nutzer_innen ein schnelles Onboarding. Mit ihrer Hilfe können sie vorkonfigurierte Umgebungen automatisch in Betrieb nehmen und ihre Anwendungen skalieren, ohne dafür physische Hardware kaufen oder betreiben zu müssen – alles schnell und sicher direkt in der Cloud.
Diese Plattform bietet zudem die Möglichkeit, andere vorgefertigte Dienste zu nutzen, die sich ebenfalls in wenigen Minuten einrichten lassen. Wir garantieren dabei einen Service aus einer Hand: Das Kubika-Team der AUDI AG leitet das Kubernetes Competence Center, ist Partner der Cloud Native Computing Foundation (CNCF) und entwickelt gemeinsam mit RedHat OpenShift das Kubika-O-System. Kubika wird vom G/FP-5-Team für Cloud- und Plattformdienste unterstützt und betrieben.
Aber wir leisten noch mehr für die Transformation in der virtuellen Welt: Kubika ist nämlich nicht die einzige Entwicklung, die den digitalen Wandel innerhalb des Unternehmens unterstützt. Um die Digitalisierung auf die nächste Stufe zu heben, ist der schnelle und sichere Zugriff auf Daten und deren Verfügbarkeit die Grundvoraussetzung. Damit dies zukunftsfähig und flexibel gewährleistet ist, haben IT-Mitarbeitende und Verantwortliche des Volkswagen Konzerns im Jahr 2022 gemeinsam einen Datenintegrationsdienst (Datalayer) konzipiert und installiert: den Plant Connectivity Service. Dieser ermöglicht eine stabile, sichere und flexibel erweiterbare Übertragung von Daten zwischen verschiedenen IT-Systemen und Plattformen – unabhängig davon, ob sich die Systeme im Serverzentrum von Audi Hungaria oder auf einer anderen Plattform des Konzerns befinden.
Der Plant Connectivity Service ermöglicht Audi Hungaria unter anderem die Anbindung an die „Digital Production Platform” (DPP); das ist eine innovative Plattform, die Volkswagen zusammen mit Amazon Web Services (AWS) und Siemens entwickelt hat. Bei der Planung innovativer Softwareanwendungen auf Basis der DPP geht es vor allem darum, dass die Daten allen Produktionsstandorten schnell und flexibel zur Verfügung stehen. Insgesamt bietet die DPP moderne und flexible Cloud-basierte Services zur Unterstützung und Entwicklung von Produktionsprozessen – ein weiterer Beitrag zur Steigerung unserer Effizienz.
Neben diesen Aktivitäten arbeitet unsere IT auch zusammen mit der Finanzabteilung aktiv an zukunftsfähigem Process Mining, unterstützt durch einen Spezialpartner. Das führt zu schnelleren und effektiveren Geschäftsprozessen und damit zur Optimierung von Projektabarbeiten. Was die Projekten in anderen SCC-Bereichen anbelangt: Wir haben im Bereich Controlling Fahrzeugsysteme unser Aufgabenportfolio um innovative Zukunftstechnologien erweitert, damit wurde der Anteil an E-Mobilität-Projekten in 2022 auf 30 Prozent erhöht. Besonders stolz sind wir darauf, dass unsere Qualitätssicherung der Antriebsfertigung mit Dienstleistungen im Projektmanagement projektbezogene Verantwortung für die sportliche Marke Lamborghini übernimmt.