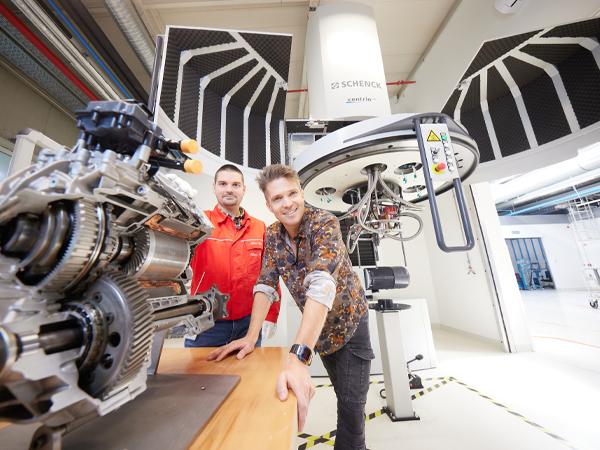
Achtung, Kamera läuft!
Ein Blick hinter die Kulissen der Technischen Entwicklung
Zwei spannende Tage in der Technischen Entwicklung (TE): Wir sehen einen Klimaprüfstand, der Extremwetter nachstellen kann, einen Raum, der jeden Schall schluckt, und High-tech-Festigkeitsprüfstände, die den stärksten Rotor zum Bersten bringen können. Solche Geheimnisse der TE werden vom bekannten Vlogger Csaba Gyetván und seinem Team für eine Dokumentation des Discovery Channels zusammengetragen. Kommen Sie mit „behind the scenes“ – eine ganz besondere Werksbesichtigung kann beginnen!
Autos sind unsere zuverlässigen Begleiter im Alltag; diese Überzeugung ist schon fast eine Selbstverständlichkeit. Aber wie viel Know-how muss gebündelt werden, wie viele Hunderttausende von Testzyklen müssen durchgeführt werden, bis garantiert ist, dass Millionen von Starts und Stopps, Beschleunigungen und Bremsungen reibungslos ablaufen? Daran denkt kaum ein Autofahrer. Denn wir sehen nicht, wie der Akustikingenieur in der Prüfkabine mit High-End-Technologie den gewünschten Geräuschpegel der Karosserie prüft. Wir wissen auch nicht, dass die ideale Motorfunktion unseres Autos das Ergebnis von Tausenden Arbeitsstunden der Simulationsingenieure vor dem Monitor ist. Doch ein Blick hinter die Kulissen gibt uns jetzt neue Einblicke.
In unserer Technischen Entwicklung – dem drittgrößten Entwicklungszentrum der AUDI AG – sind wir schon beim morgendlichen Kaffee mitten in einer lebhaften Diskussion: Fotografen und Kameraleute stimmen sich noch einmal mit Csaba Gyetván über die vorher festgelegten Drehorte ab. Der TV-Moderator der „How It`s made”– Videos und Vlogger dreht mit seinem Team für den Discovery Channel die nächsten Folgen der Serie „Made in with Gyetván Csaba”; hier in der TE von Audi Hungaria. Am Montagmorgen um neun Uhr sind das Team und seine Technik startklar – Kamera läuft:
Ruhe, bitte!
Wir starten in der Gesamtfahrzeugentwicklung. Zwischen Festigkeits- und Rollenprüfständen nähern wir uns unserer ersten Station: dem Akustikraum. Von außen sieht der aus wie ein riesiger Panzerschrank: Eine 50 Zentimeter dicke Tür verschließt den Raum mit Schallabsorbern. Die verhindern, dass die Schallwellen von den Wänden reflektieren. Selbst das Belüftungssystem ist schallgedämpft – und der Raum hat zudem eine geräuscharme Abgasabsaugung. Schließlich werden zuweilen auch laufende Motoren getestet. Wozu das alles? Für das große Ziel, die durch den Betrieb der Fahrzeuge entstehenden Geräusche maximal zu reduzieren, indem sie vom Fahrgastraum abgeschirmt werden. „Denn wenn wir nicht geschickt sind, würde die Karosserie ein gut funktionierender Lautsprecher werden”, erklärt Dr. István Antal Horváth. Der Akustik-Entwicklungsingenieur steht neben der Rohkarosserie eines Q3 Sportback und wertet die Daten des auf die Karosserie gerichteten Laserscanners aus. Aus denen wird ein Vibrationsbild erstellt. Mal ist der Raum erfüllt von Geräuschen wie in Andrei Tarkowskis Klassiker „Solaris“, mal erklingt ein süßes Schlaflied, während István alle Daten aufzeichnet.
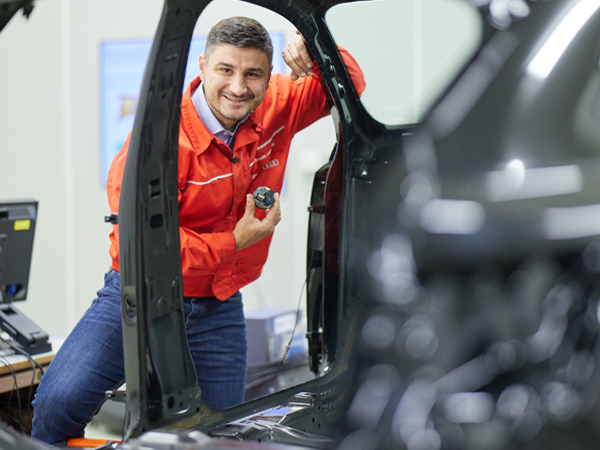
Wenn wir nicht geschickt sind, würde die Karosserie ein gut funktionierender Lautsprecher werden.
Achtung, Zentrifugen im Einsatz
Aus fast gespenstischer Stille kehren wir zurück in die Welt des Lärms: zu den Schleuderprüfständen (SPS), nur wenige Schritte vom Akustikraum entfernt. Die jeweils vier bis fünf Meter hohen Maschinen werden für die Drehimpulsprüfung, die Zyklusprüfung und für die Berstprüfung der Rotoren eingesetzt. In den Zentrifugen simulieren diese Tests die Reaktionen auf verschiedene Situationen im Leben eines Audis – und sogar Belastungen über die gesamte Laufzeit. Dazu untersuchen die Experten das Festigkeitsverhalten des Rotors, des Herzstücks eines Elektromotors. Entwicklungsingenieur Mátyás Dobos stellt uns die Testmethoden vor. „Bei der Drehimpulsprüfung messen wir die rotatorische Aufweitung des Rotors. Wir erzeugen Betriebsbedingungen in der Zentrifuge und zeichnen dann mithilfe von Sensoren Daten mit 180.000 Messpunkten pro Sekunde auf. Der Zyklustest ist anders: In dieser Phase wird der Rotor zwei Wochen lang 24 Stunden am Tag gedreht. Dabei werden Umdrehungen erreicht, die deutlich über jene unter Kundenbedingungen hinausgehen. Wir wollen sehen, wie sich der Rotor unter extremer Belastung verhält. Und der Sinn dieses Tests ist es, ihn bis zum Bruch – wir sprechen hier vom Bersten – zu belasten.“ Extreme Bedingungen sind nötig, um einen mehrere Kilo schweren Stahlkörper zum Bruch zu bringen! Sobald der Rotor befestigt ist, wird die Zentrifuge geschlossen. MitHilfe eines Keramik-Heizstrahler wird der Rotor auf 130 bis 180 Grad Celsius aufgeheizt und danach temperiert. Der Rotor wird so lange beschleunigt, bis es mit extrem hohen Umdrehungen im Vakuum plötzlich nachgibt. An diesem Punkt injiziert das System Stickstoff in die Zentrifuge, um einen Funkenbildung zu verhindern. Drei halbtonnenschwere Stahlringe schützen die innere Schicht der Zentrifuge im Abstand von wenigen Zentimetern vor einem Durchschlag. Die Rotorteile werden somit während einem Berstfall praktisch in den innersten Ring eingebettet. Der Aufwand muss auch sein. „Denn die beim Bruch freigesetzte Energie ist so groß, dass sich der erste Schutzring aus seiner Position bewegen kann. Berechnungen haben ergeben, dass Teile des Rotors mit fast Mach 1 – also Schallgeschwindigkeit – auf den Ring treffen“, gibt Mátyás eine Vorstellung von den Größen, die im Inneren wirken. Die beiden Zentrifugen sind ein großer Entwicklungsschritt: Bisher konnte der Volkswagen Konzern solche Versuche nur mithilfe externer Firmen durchführen; jetzt ist die Prüftechnik „Made in Hungary“. Übrigens, liebe Kundinnen und Kunden – keine Angst: Ein solch extremer Prozess kann im Normalbetrieb niemals stattfinden. Die Elektroantriebe arbeiten dort bei deutlich niedrigeren Drehzahlen.
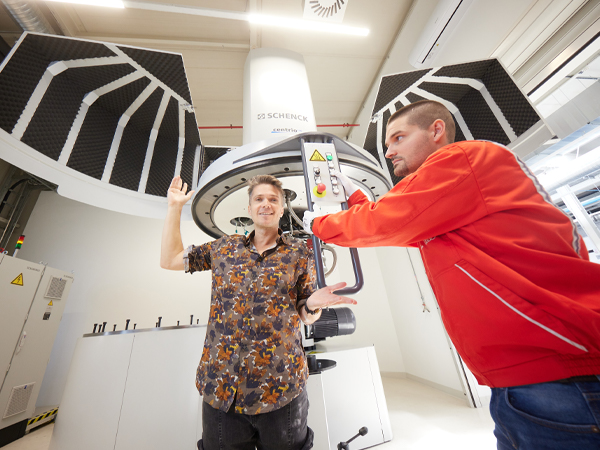
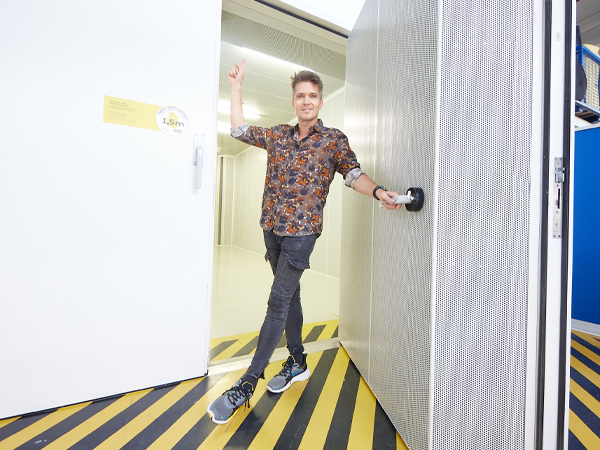
Erfüllt das System die
Eigenschaftsanforderungen?
Unser nächster Schauplatz ist der Rollenprüfstand. Beim Betreten eines Raumes bietet sich uns ein sportlicher Anblick: Drei Fachleute beobachten auf einem Monitor einen stattlichen Porsche. Das „Testobjekt“ ruht auf einem Rollenprüfstand, während zwei riesige Ventilatoren einen künstlichen Fahrtwind erzeugen. Das Auto scheint so über Berg und Tal zu fahren, während die Geschwindigkeitswechsel an den Stop-and-go-Verkehr in der Stadt erinnern. Möglich macht´s der 160 Tonnen schwere Prüfstand: Er ruht auf Stahlfedern, die in den Boden eingelassen sind. Dort befinden sich auch die Elektromotoren, die das Gebläse in Gang setzen – sie können eine Windgeschwindigkeit von 130 Stundenkilometern erzeugen. Ziel der Prüfung ist es, die Aufhängung der Abgasanlage und der neuen Befestigungsbauteile unter verschiedenen Belastungsbedingungen zu überprüfen – und das teilweise bei eine Höchstgeschwindigkeit von Tempo 280. Bestimmte Teile sind dabei mit Dehnungsmessstreifen und Beschleunigungsmessern ausgestattet. Die Ingenieure prüfen überdies, was für Geräusche und Vibrationen während der Fahrt entstehen. Auch hier ist die Wand mit schallabsorbierendem Material verkleidet. Denn akustische Messungen führen die Fachleute auch auf dem Rollenprüfstand durch, wo das Rollgeräusch des Fahrzeugs über Stunden oder sogar Wochen verfolgt wird.
Die Ingenieure prüfen, welche Geräusche und Vibrationen während der Fahrt entstehen.
Motorsteuerung? In Ordnung.
Das „Hardware-in-the-Loop“-Labor (HiL) erinnert an einen Serverraum, vollgepackt mit Rechnern. Hier werden wir von Gábor Ferenc Takács und László Kajcsos empfangen. Sie sind diejenigen, die mit HiL-Prüfständen bereits zu einem frühen Zeitpunkt in der Entwicklung testen, wie die Motorsteuerung im Gesamtverbund vernetzt ist. „Durch dieses Vorgehen können viel früher Erkenntnisse gesammelt und in die weitere Entwicklung eingebracht werden, als dies mit realen Fahrzeugtests der Fall wäre. Diese Maschinen führen sowohl sensorische als auch Belastungssimulationen durch und testen die Kopplung mit der Steuereinheit“, erklären die Simulationsingenieure. Hightech für die höchsten Ansprüche – dieselbe Technologie kommt auch in der Luft- und Raumfahrt zum Einsatz. Der Tag neigt sich dem Ende zu – und uns schwirrt der Kopf vor Informationen und Eindrücken. Aber auch schon in Vorfreude auf morgen: Dann verspricht das Team der Technischen Entwicklung Fahrzeugantriebe ein kompaktes Programm und ähnlich faszinierende Erlebnisse.
So entstehen die Antriebe
Wir beginnen unseren zweiten Tag im Bürogebäude der Antriebsentwicklung. András Doór, Fachkoordinator des Akustikteams, kommt schnell zum Punkt: „Die AUDI AG erstellt das Konzept, wir entwickeln und fertigen den Antrieb hier in Győr – und am Ende des Prozesses steht das fertige Produkt.“ Während wir uns unterhalten, gehen wir durch die Aula, wo wir an einem Audi S5 3.0 TFSI vorbeikommen. Da wird der Schritt deutlich langsamer … wer will das Schmuckstück nicht bestaunen? Doch wir müssen weiter. Das Programm ist dicht gedrängt. Es geht in die Konstruktionsabteilung. Dort werden die Bauteile in einer dreidimensionalen Umgebung entworfen. Die Teams hier konstruieren jedoch nicht nur, sondern verfolgen auch den Lebenszyklus der Teile. Dazu stehen sie mit den Versuchsingenieur_innen, der Planung, der Beschaffung, der Controlling, der Qualitätssicherung, der Logistik, der Produktion und dem Hersteller in engem Kontakt.
Wir werden von Konstrukteur Dániel Michl erwartet, der sich mit elektrischen Antrieben beschäftigt. Als wir ankommen, testet er gerade den Antriebsstrang eines allradgetriebenen Audi e-tron auf dem Monitor. Auf Nachfrage unseres Reporters Csaba beginnt er, über die typischen Arbeitsabläufe zu sprechen. „Grundsätzlich arbeiten wir an der Konstruktion. Doch was unsere aktuelle Aufgabe ist, hängt vom Projekt ab … Ein Projekt kann sowohl mit der Weiterentwicklung eines früheren Verbrennungs oder E-Antriebs starten, als auch ganz von vorn beginnen. In diesem Fall entwickeln wir nicht das Modell der Vorgängergenerationen weiter, sondern ein komplett neues Konzept. Natürlich nutzen wir auch im zweiten Fall die Erfahrungen aus den bisherigen Konzepten. Für unsere Kundinnen und Kunden sind Leistung, Kosteneffizienz und natürlich die Reichweite der Elektroautos nach wie vor von größter Bedeutung”, sagt er. All diese Faktoren berücksichtigt das Team bei der Entwicklung genau.
Absolut wie im Kino!
Vorsprung durch Technik – und damit ein kleiner Exkurs aus den heiligen Hallen der TE – steht nun als Intermezzo auf dem Programm: Dazu begleitet uns Dániel noch in die Elektroantriebs-Montage, eine der spektakulärsten Sehenswürdigkeiten für jeden Fan der neuen Mobilität. Als wir eintreten, sind wir fasziniert vom Anblick der elektrischen fahrerlosen Transportfahrzeuge (FTF): In der Art von Maschinen aus der Welt von „Star Wars” fahren die 36 FTF völlig autonom und ohne menschliche Aufsicht durchs Werk. Wir werden sie bald noch näher kennenlernen…
Projektleiter Attila Józsa erzählt uns, dass neben den FTF-s 330 bis 340 Kolleg_innen in drei Schichten im Montagewerk arbeiten. Hier wird der Stator für den Antrieb des Audi e-tron SUV hergestellt – 530 Stück pro Tag verlassen die Fertigung. Im nächsten Schritt werden der Rotor, die Lager, die Dichtungen und andere notwendige Komponenten in den Stator eingebaut, schließlich noch das Getriebe. Der fertige Antriebsstrang geht anschließend auf den Prüfstand – und schließlich nach Brüssel, wo er in das batteriegetriebene Auto eingebaut wird. Doch zurück zu den Transportfahrzeugen, den sogenannten „Hunden“. Ohne sie würde die Produktion heute nicht so reibungslos laufen: Sie transportieren Teile und Antriebskomponenten zwischen den Produktionsinseln; wenn wir ihnen in die Quere kommen, warnen sie uns. Mit einer einzigen Akkufüllung können die FTF drei bis vier Stunden auf den ihnen zugewiesenen Fahrspuren fahren und sich dann selbstständig an das Ladegerät anschließen. Alle Maschinen der Montage geben Informationen zudem an ein zentrales Programm weiter. Dieser Leitstand weist die Transportfahrzeuge daraufhin an, welche Produktionsinsel sie als Nächstes anfahren sollen. Ein ganz exklusives Erlebnis; denn diese Technologie ist in vielen anderen Autowerken noch Science-Fiction. In Györ ist es Science-Fact!
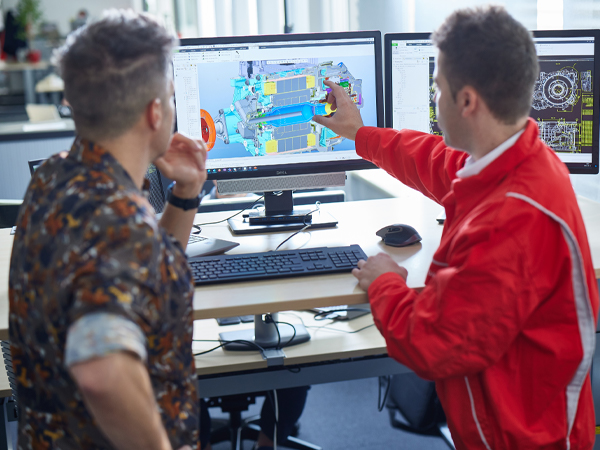
In die Konstruktionsabteilung werden die Bauteile in einer dreidimensionalen Umgebung entworfen.
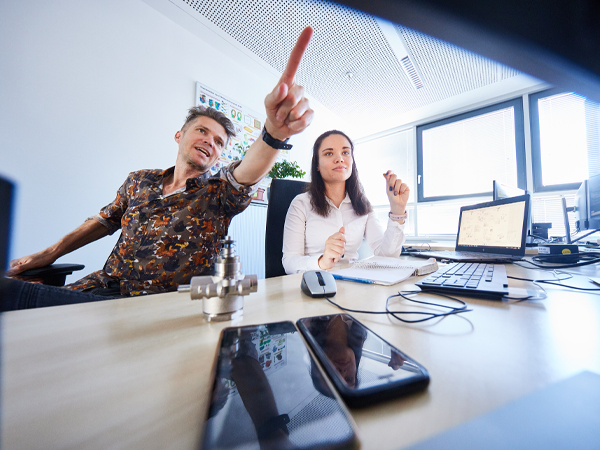
Simulationen ersetzen Tests
Zum Staunen bleibt aber wenig Zeit. Denn nach ein paar Minuten stehen wir schon vor dem Monitor von Beatrix Sipos. Die Ingenieurin führt numerische Simulationen der Belastungen durch, die im realen Gebrauch auftreten werden. Sie und ihr Team suchen nach Antworten auf die Frage, ob ein Bauteil unter einer bestimmten Belastung bricht. „Diese Arbeit spart uns eine Menge Ressourcen, Zeit und Geld“, sagt sie ganz nüchtern. Die numerische Simulation ersetzt einen Teil der Prüfstand- und Fahrzeugtests, indem sie die zu erwartende Lebensdauer der einzelnen Teile vorhersagt.
Noch ein Akustiktest
Wenn es jedoch einen Ort gibt, wo man reale Tests nicht einsparen kann, dann ist es der akustische Prüfstand. Versuchsingenieur Viktor Rőfös-Horváth und unser alter Bekannter András Doór erklären den Kern des Tests in einem schalldichten Raum an einem Lamborghini-Motor. Hier testen sie mit Beschleunigungssensoren und Mikrofonen stundenlang den Geräuschpegel und Schwingungen (Vibration) des laufenden Motors. Die Experten können anhand der Ergebnisse aus verschiedenen Betriebszuständen feststellen, ob ein Motor – mal direkt vom Band, mal ausgebaut aus einem fertigen Auto – akustisch einwandfrei ist; und falls nicht, welcher Teil des Motors das Problem darstellt.
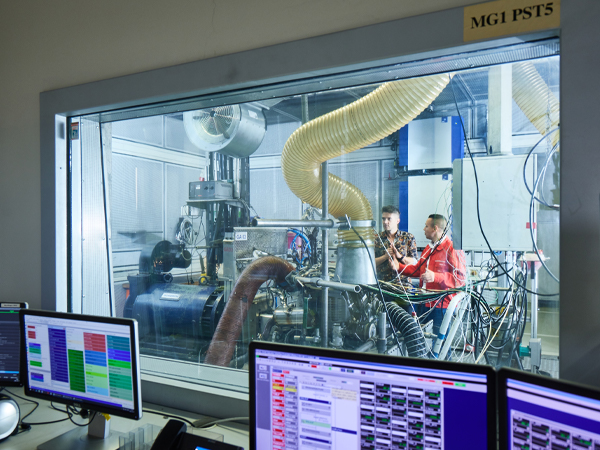
Extreme Bedingungen
Die letzte Station unserer Werksbesichtigung und der Dreharbeiten befindet sich ebenfalls im Testzentrum, dem Ort der Langzeittests, wo in verschiedenen Kabinen Gluthitze auf Eiseskälte folgt: In Klimakabine 14 werden bei Temperaturen zwischen plus 40 und minus 40 Grad Celsius Klimatests an den Betriebsmitteln des Hybridantriebs durchgeführt. Wir kommen bei 28 Grad minus im Test von Ákos Balics an. Der Entwicklungsingenieur erklärt, dass die Nachfrage nach Hybridantrieben in den nordischen Ländern viel höher ist – einer der Gründe, warum die Tests bei diesen Temperaturen durchgeführt werden. Da der Motor in Hybridfahrzeugen häufig abgestellt und neu gestartet wird, sind extreme Tests mit häufigen Änderungen der Temperatur und anderer Parameter erforderlich. In der Kabine startet und stoppt ein Motor alle paar Sekunden – und das 24 Stunden, rund um die Uhr. Es gibt Motoren, die so in zwölf Wochen 100.000 Kilometer zurücklegen können. „Dies ist einer der komplexesten Start-Stopp-Tests. Das System führt täglich 3.000 Start-Stopp-Zyklen durch – und der Test endet bei 250.000 Zyklen. In der Zwischenzeit wechseln wir natürlich die Öl- und Luftfilter sowie die Zündkerzen und überwachen die Motorcharakteristik, die Frequenzen, das Motormanagement und die Komponenten. Auf während der Versuche aufgetretene Probleme müssen wir sofort reagieren. Kein Arbeitstag gleicht dem anderen, genau das macht den Reiz des Berufes aus“, hören wir zu unserer Überraschung vom Techniker vor dem Monitor des Prüfstands.
Am Ende unserer zweitägigen Entdeckungstour stehen faszinierende Eindrücke und ein klares Fazit: Audi Hungaria geht nicht vom Gas – im Gegenteil: In den kommenden Jahren wird das Unternehmen einen zweistelligen Euro-Millionenbetrag in die Technische Entwicklung investieren. Mit diesem Geld wird ein neuer Prüfstand für die Entwicklung elektrischer Achsantriebe und der dazugehörigen Übertragungen installiert und die bestehende Prüfstand-Infrastruktur aktualisiert: ein neuer großer Beitrag zur Zukunft der Mobilität – aus Győr für die Welt.